Frontline Fundamentals: HP Principle Five: “Why” Works
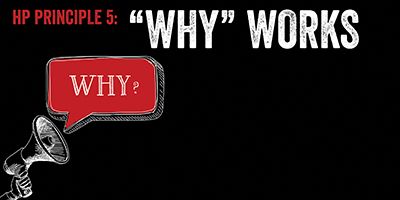
Frequently I am asked about the qualifications of a safety professional, what makes a good leader and what it takes to work safely. My answer to each question is the same – you must get really good at asking and understanding “why.” At a minimum, you must ask and understand why rules, procedures and work methods are in place; why performance, behavior and results are occurring; and why past events, incidents and errors happened.
If you become really good at asking and understanding “why” in those areas, you will be able to employ human performance (HP) principle five, which states that events can be avoided through an understanding of the reasons why mistakes occur and application of lessons learned from past events or errors. This principle reminds me of an adage most of us have heard before: Fool me once, shame on you, fool me twice, shame on me. It also reminds me of a definition of insanity – doing the same thing over and over and expecting different results. I like to summarize HP principle five by saying simply, “‘Why’ works.”
Not long ago, my son was trying to park a golf cart in the cart shed. He got upset because he was in a repeated cycle of turning too early, almost hitting the shed, backing up and trying again. I let him go through that cycle of repeating the same mistake a few times and then calmly said, “Try again, but do something different this time.” He tried again and still turned too early but improved. The next time he turned too late. After a few more tries, he finally got the cart in the shed without hitting anything.
He got the cart in the shed because, without knowing it, he used HP principle five. He shifted from expecting a different outcome with the same behavior to understanding why the situation was occurring and trying something different until he achieved his desired outcome. Now, he applies the lessons he learned and usually parks the cart successfully on his first try.
Key Points
I share that story to reinforce use of the self-checking tool and to deliver these key points about the application of HP principle five:
- Stop and define your desired outcome.
- Think about how you will achieve your desired outcome.
- Act to ensure your desired outcome happens, and that is all that happens.
- Review your performance, adapt and repeat until your desired outcome is achieved.
Take a moment to think about that last step above: review. In that step, essentially you take a very critical look at performance – notice I didn’t say “results,” and remember that Performance = Behavior + Results – and determine what was good, what could have been better and what you will do in the future. In relation to safety, I hope the lessons are learned and applied through near-miss and near-hit reports, good catches, job site observations and inconsequential errors. Note that the alternative is to learn lessons through incidents, including injuries.
HP principle five works – and works well – when we focus on why performance is occurring, what the desired outcome is and how we will act in the future. It very rarely works when we focus on “who.”
To learn more about HP principle five, I challenge you to read about it in the U.S. Department of Energy’s Human Performance Improvement Handbook and in just about anything written by James Reason. Be sure to understand the culpability matrix and determine if you ever fall into the blame cycle – you can easily look up both topics in any online search engine. I also invite you to attend our free webinar on this subject on November 14 (see breakout box for more information).
I’ll leave you with this thought: Very rarely does someone intend to get hurt, and usually actions leading up to an injury make sense at the time in the environment. It’s easy to blame someone when they get injured. It takes a little more effort to understand their behavior and why it occurred. That extra effort is worth it to learn lessons that can be applied to prevent future recurrence. Now, I’ll make any Dallas Cowboys fans happy by closing with this quote from Jimmy Johnson: “The difference between ordinary and extraordinary is that little extra.”
About the Author: David McPeak, CUSP, CET, CHST, CSP, CSSM, is the director of professional development for Utility Business Media’s Incident Prevention Institute (www.ip-institute.com). His experience includes operations management, safety and training roles. McPeak holds multiple safety and training certifications and has received numerous awards. He also has served as chairman of Task Team One of the OSHA ET&D Partnership, as a member of Incident Prevention’s editorial advisory board and as a member of the North Carolina Apprenticeship Council. Reach him at david@utilitybusinessmedia.com.
About Frontline: The Frontline program provides interactive, engaging classroom training that empowers employees to become better utility safety leaders. Subject matter experts facilitate the learning process and cover four areas – safety leadership, incident prevention, human performance, and standards and operations – critical to safety success. Visit www.frontlineutilityleader.com for more information.
*****
Webinar on HP Principle Five: “Why” Works
November 14 at 3 p.m. Eastern
Visit www.frontlineutilityleader.com for more information.