Frontline Fundamentals: Human Performance Implementation
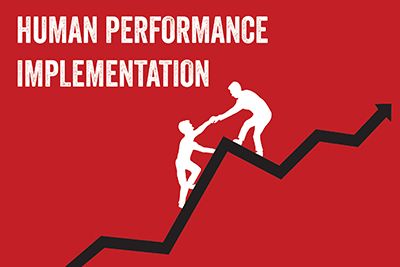
For all of 2018, this column and its associated webinars have focused on human performance (HP). I have thoroughly enjoyed and learned a lot from the guest speakers who participated in the webinars, as well as the readers and webinar participants (you) who have been engaged, shared their experiences, and asked intelligent and challenging questions.
In this article, I will wrap up the HP series by reviewing key points, outlining proven strategies about HP implementation and inviting you to our next webinar – scheduled for January 16 – that I am really excited about because we will have a panel of experts gathered to explain HP implementation, address your concerns and answer your questions.
HP Review: Principles and Key Points
Principle One: People are fallible, and even the best make mistakes.
People screw up. We make mistakes, and often we are not aware of them. That is a real problem, especially with regard to safety. Rarely are our errors and their undesired consequences intentional, and most errors have no immediate negative consequences. Because of this, your safety program must acknowledge that people will make mistakes. With that acknowledgement, we can use HP tools to reduce errors and manage controls.
Principle Two: Error-likely situations are predictable, manageable and preventable.
You have a crystal ball. Knowledge gives you power, and while you cannot use HP to predict exactly when incidents will happen, you can predict situations in which incidents are likely.
Understand that we cannot eliminate error precursors such as time pressure, but we can always manage them by not allowing them to negatively impact our decision-making. For example, STAR – which stands for Stop, Think, Act, Review – is a simple yet extremely effective tool that helps us manage error-likely situations and prevent negative impact on our decision-making.
Principle Three: Individual behavior is influenced by organizational processes and values.
You and your organization cannot outperform each other. We need to align ourselves as a TEAM (Together Everyone Accomplishes More) with common expectations and values to stay safe.
Coupled with the other principles, Principle Three helps us acknowledge that incidents occur more often due to error-likely situations than error-likely individuals, and that error-likely situations often are created by latent organizational weaknesses.
Principle Four: People achieve high levels of performance because of the encouragement and reinforcement they receive from leaders, peers and subordinates.
People influence each other. That can be good or bad, especially if you are in a leadership position. Reinforce desired behaviors with positive, immediate, certain and significant consequences. Do this effectively and you can expect desired behaviors leading to desired performance, TEAMwork, increased communication resulting in mutual understanding, better morale and increased retention rates.
Principle Five: Events can be avoided through an understanding of the reasons why mistakes occur and application of lessons learned from past events or errors.
“Why” works. Incident investigations should focus on how and what – not who. You must learn, understand and apply lessons to prevent recurrence, and hopefully you do this during observations and inconsequential errors. But it’s not just about incident investigations. Work planning tools such as pre-job briefings should include a discussion about similar jobs in the past, what has worked well and what could have been better.
The test of HP implementation is incident recurrence. All five principles combined allows you to use the culpability matrix to focus on systems without forgetting about human factors.
Implementing HP
While there is no exact implementation strategy or a precise roadmap, here are proven action items used by individuals and organizations that have successfully implemented HP.
- Tools such as self-check, communication, work planning and verification practices are incorporated into the design and execution of tasks, processes and programs.
- Leaders lead people the way they are, not the way they wish they were.
- Everyone is trained on HP, and there are HP champions and trainers in the frontline workforce.
- The TWIN Model of Error Precursors is used in work planning and incident investigations.
- Incident investigators receive specialized training on HP with an intense focus on Principle Five.
- Resources are focused on improving systems, latent organizational weaknesses, processes and culture.
- People are not fixed – they are trained and developed through coaching, feedback and mentoring.
- There is TEAMwork with management commitment to worker-driven safety.
To summarize, HP is successfully implemented when people are viewed not as problems but as assets – the most valuable assets in the organization. Additionally, HP is not an excuse to make mistakes; it is a system that clearly communicates expectations, increases accountability, reduces errors, improves reliability and quality, and manages controls.
It is important to note that HP and safety are related but not the same. HP is intended to protect systems from people, but it is useful for protecting people as well. HP should be part of – but not the only component of – your safety program.
HP principles work if you believe in them, and HP tools work if you understand and use them.
Upcoming Webinar
We have assembled a panel of HP experts for our January 16 webinar who will discuss HP implementation, address your concerns and answer your questions. You may never have a better opportunity to learn how HP can work at your organization or about the challenges you will face selling and implementing HP. The webinar is going to be awesome, it’s going to be fun, it’s going to be valuable, and it’s free – don’t miss it.
About the Author: David McPeak, CUSP, CET, CHST, CSP, CSSM, is the director of professional development for Utility Business Media’s Incident Prevention Institute (www.ip-institute.com). His experience includes operations management, safety and training roles. McPeak holds multiple safety and training certifications and has received numerous awards. He also has served as chairman of Task Team One of the OSHA ET&D Partnership, as a member of Incident Prevention’s editorial advisory board and as a member of the North Carolina Apprenticeship Council. Reach him at david@utilitybusinessmedia.com.
About Frontline: The Frontline program provides interactive, engaging classroom training that empowers employees to become better utility safety leaders. Subject matter experts facilitate the learning process and cover four areas – safety leadership, incident prevention, human performance, and standards and operations – critical to safety success. Visit www.frontlineutilityleader.com for more information.
*****
Webinar on Human Performance Implementation
January 16 at 3 p.m. Eastern
Visit www.frontlineutilityleader.com for more information.